Machined Plastic Parts
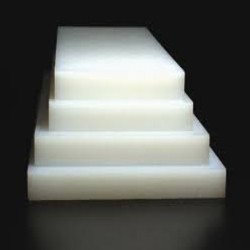
About UHMW and HDPE UHMW(Ultra High Molecular Weight) polyethylene plastic is known for its exceptional impact strength, making it one of the most durable thermoplastics available. It also offers outstanding abrasion resistance and tensile strength. Among all polyethylene materials, UHMW stands out with the highest impact strength. It outperforms carbon steel by a ratio of 10 to 1 in some applications. Additionally, it resists stress and cracking while boasting a low coefficient of friction, making it self-lubricating. These properties make it ideal for sliding applications, rough surfaces, or any scenario where reducing friction is essential. HDPE (High Density Polyethylene), while slightly lower in tensile strength compared to UHMW, offers excellent chemical resistance and minimal moisture absorption. This material is widely used in industries that demand impact resistance, high tensile strength, and resistance to chemicals and corrosion. In machining applications, it achieves a finer finish than UHMW, though both materials are easy to machine. Today, various grades of UHMW and HDPE are available to meet specific application needs. For example, anti-static grades of UHMW (AS/UHMW) are used to produce parts that prevent the build-up of electrical charges, making them ideal for sensitive environments. A.L.Plastics | Marion Collection | Acrylic Depot
Custom Plastics Machining
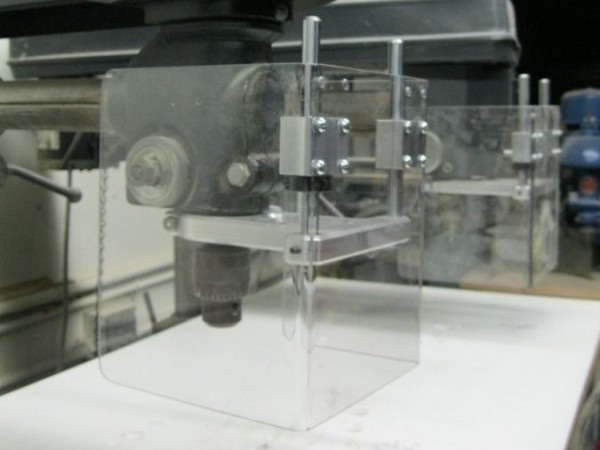
Custom Plastics Machining: What to Look for in a Supplier 1. Technology base It will always be preferable to work with suppliers who have the latest CNC production technology allied to skilled workers. These suppliers will be able to produce parts to close tolerances while keeping part quality and finish consistently high. 2. Materials expertise and selection There are a wide variety of plastic materials available on the market today. The best suppliers know their materials and know the latest materials available on the marketplace. These suppliers will be able to provide superior guidance on material selection, ensuring that the right material is chosen for a given application. Choosing the wrong material, or a material which is not exactly right, can result in misapplication challenges later on. 3. Application expertise in custom plastics machining Material knowledge is one thing, application knowledge is another. The latter should always precede the latter. Choose a supplier who knows how to undertake a comprehensive application review to determine how a finished part will be used. A good application review will identify all the requirements that the finished part must satisfy, and is critical for ensuring that the right material is chosen. In addition, some suppliers will specialize in serving a narrow range of industry applications, while other suppliers will serve a broader range. It is important to choose a supplier who has experience in serving your particular application – choosing a supplier with limited experience in servicing your specific application may increase the risk of misapplication issues arising post-sale. A.L.Plastics | Marion Collection | Acrylic Depot