Tips and Tricks for CNC Machine
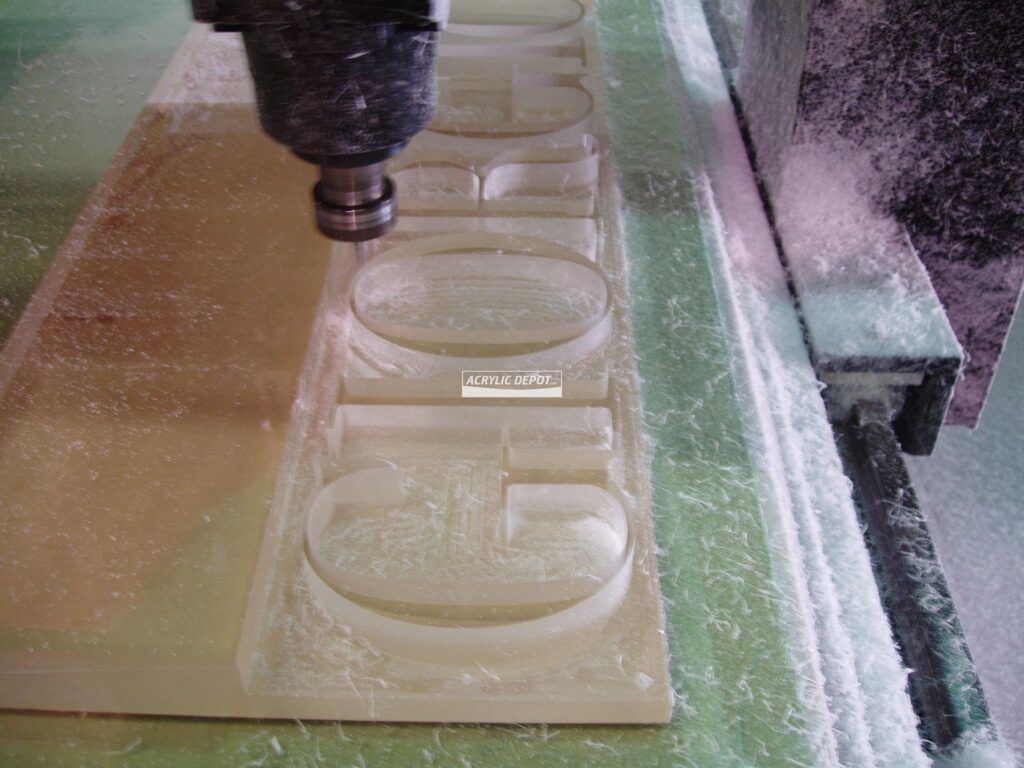
1. Have some quality Bits Avoid purchasing cheap, low-quality Bits. Get some good bits from a well-known brand with reasonable prices. This will make a huge difference in producing quality parts and will eliminate tons of unnecessary problems that can occur by using cheaper tools. 2. Prevent chip buildup by misting set up for coolant The siphon-based and micro-drop are two types. The siphon system completely atomizes the coolant into an aerosol, which can be messy. The micro-drop system pressurizes the coolant, keeping the coolant and air in separate chambers until they hit the tip of the tool. 3. Speeds and Feeds calculator device for accurate results CNC machining is a different ballgame from manual machining and it’s very important to get your feeds and speeds correct, right from the start. So, a feed and speeds calculator is essential. 4. A set of parallels and a clamping kit A nice clamping kit will mount your vise to the T-slots of your table. Finally, use a decent set of parallels to keep your workpiece parallel or evenly raised, allowing the cutting tool or spindle to pass over it smoothly. 5. Manual Data Input (MDI) You’ll save a lot of time and increase your productivity by using the Manual Data Input (MDI), which is accessed via the MDI keypad on your CNC machine’s control panel. It requires very little learning and will save a lot of time. You can set some basic g-codes and adjust your X, Y and Z coordinates, move your axes, and the machine will move rapidly after you’ve inputted the information. This rapid movement of the machine is referred to as “Rapids.” You want that cutter to go where you want it to go.
Laser cutting process for acrylic ( Lucite ) sheets

1. Define Your Cutting Expectations Before cutting acrylic, you must first determine your expectations for the final product. Does the end result need a flame-polished, optical-quality finish? Or is the part intended for mechanical use, where edge quality is less critical? This decision will help you choose the appropriate cutting method. For example, if edge quality isn’t a priority, you can save significant time by opting for a less refined cut. 2. Understand the Laser Cutting Process Laser cutting works by vaporizing the solid acrylic material. The laser’s energy causes the acrylic to transition from solid to liquid and then to vapor. This process involves minimal chemical degradation, ensuring a clean cut. However, laser cutting generates a large amount of vapor, which requires an efficient vacuum system to remove it. Importantly, the vapor produced during laser cutting is highly flammable. To prevent accidents, never leave the laser system unattended when cutting acrylic. 3. Use Airflow to Enhance Cutting Quality A gentle stream of air or nitrogen helps blow vapor away from the cutting area. This airflow not only prevents the vapor from igniting but also solidifies the liquid along the cut line. When done correctly, it creates a glossy, flame-polished finish on the cutting edge. However, excessive air pressure can disrupt the solidification process, resulting in a frosted or wavy edge. To avoid this, use an air assist pump with a variable pressure regulator. This allows you to control the airflow and achieve the best results. 4. Choose High-Quality Materials The foundation of a good cut lies in the quality of the material. Using name-brand acrylics ensures optimal results, as these materials are consistent and reliable. Trusted brands like Trotec offer superior performance and are recommended for achieving professional-grade cuts. Brand Manufacturer Plexiglas® / Acrylite® Evonik Perspex® Lucite Altuglas® Akemar Plazit® Plazit Quinn® Quinn Oroglas® Oroglas Types Of Acrylic There are two main types of acrylic that you will commonly encounter, cast and extruded acrylic. These two types of acrylic have slightly different chemistry and are manufactured differently, which results in vastly different cutting characteristics. For most applications, cast acrylic is probably the right material for you, but under specific circumstances extruded acrylic might have its advantages over cast acrylic. The main differences are listed in the table below. Cast Extruded General Many colours available More expensive More thickness’s available (2mm to 200mm) Greater thickness tolerance (>±5%) Less colours available Cheaper Less thickness’s available (30μm to 25mm) Lower thickness tolerance (<±5%) Laser Engraving has high contrast No bur on cut edge High molecular-weight Needs more power – higher melting point Parameters more critical for flame polishing Engraving has low contrast Sharp bur at laser cut line Low molecular-weight Needs less power – lower melting point Parameters not as critical for flame polishing Laser Power As a typical rule of thumb for every 10 Watts of power you will be able to cut 1mm / 0.04 inch of material. This will give you the ability to flame polish your cuts and give good production speed. That doesn’t mean you can’t cut 12mm / 0.5 inch with a 60 Watt laser, this is still possible, but the quality of the cut will not be nice and the process will be much slower. As a general rule, more power is always better; this gives you the versatility to cut extremely fast on thin materials and give you much better cut quality on thicker materials, peak power is the key! Frequency Depending on the material and the type of cut you would like to achieve, the frequency value will change. Flame Polished Cut Common to start with high frequencies (20 to 25 kHz) for cast acrylic. Common to start with low frequencies (2-5 kHz) on extruded acrylic. Separation Cut Common to start with frequencies (9 to 12 kHz) for cast acrylic. Common to start with frequencies (5 to 10 kHz) for extruded acrylic. By decreasing the frequency of the laser you are essentially reducing the cutting energy of the laser, this is done by reducing the amount of laser pulses over a given time frame. This can however help reduce flaming, decrease boiling but does result in slower cutting speeds. The cutting speed is defined by two factors, the quality requirements and the laser power. The typical types of cuts and their speed are shown in the image above. The light blue line represents a separation cut, which is a cut with no preference for edge quality. The second type of cut is represented by the dark blue line which is a quality cut. As you can see there is a large discrepancy in speed of the cut depending on the quality level you would like to achieve with a given thickness of material. There is also a linear increase in speed as the power of the laser increases. For example a 400W laser cutting 10mm thick acrylic will be twice as fast as a 200W laser cutting the same material. Lenses and Focus Lenses are an important factor in the cutting process of acrylics, they have different focal lengths which affect their beam radius and waist length. Without getting too technical, the lenses are responsible for the shape and quality of the cutting edge. For materials up to 20mm / 0.75 inch in thickness you should use a 2.5″ lens if the power of your laser permits this. For lasers with power levels <120 Watts you will notice a dramatic cut quality increase if you linearly increase the lens focal value as the material thickness increases. Trotec laser offers lens options from 1.5″ all the way up to 5″ versions. For materials of 3 to 6 mm (1/8 to 1/4 inch) in thickness you will be able to cut faster using a 2″ lens. For material above 20mm / 0.75 inch in thickness or if your laser power exceeds 200 Watts, using a 5″ lens will give best results. As for focus, for best results, follow these rules. Do not defocus the laser if the material you are
New Hybrid 3D CNC Machine and Printer introduces by Okuma
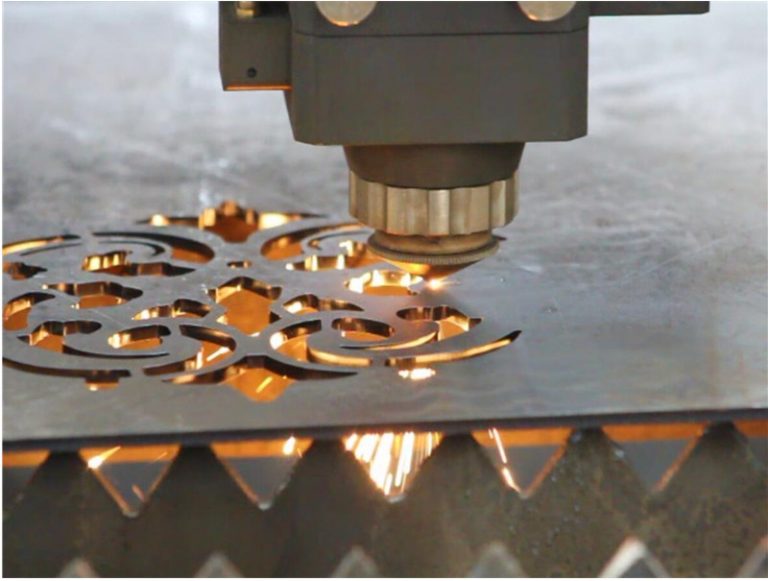
Okuma has just introduced the MU-8000V Laser EX multitasking CNC machine, which combines subtractive manufacturing with laser additive manufacturing technology. The machine uses Laser Metal Deposition (LMD), enabling it to 3D print entirely new items and add material to existing parts for repair or cladding. It can even print with multiple materials in a single build. By integrating LMD with CNC machining, this machine allows for cutting parts into various shapes, adding material, and trimming with precision. The MU-8000V Laser EX also offers mid-process inspection and repair during production. Efficiency and resolution are enhanced through infinitely variable laser spot diameters, ranging from 0.4 mm to 8.5 mm. Unlike Laser Metal Fusion, LMD technology supports mid-process part inspections, material exchanges, and coolant use within the work envelope. These features result in a faster and more flexible process. Okuma plans to expand its Laser EX line with additional features in the future. For example, laser hardening will be introduced for carbon steel materials. This process involves heating via laser emission and self-cooling, which reduces warping compared to high-frequency or flame hardening. The machines will also offer case hardening, enabling uniform hardening with less distortion. A significant advancement will include process-intensive capabilities such as turn hardening and grinding. These processes will allow cutting and grinding on a single CNC machine without requiring a setup change. Additionally, uniform-width turn hardening will be achieved with a high-output, stable laser. Case hardening on cylindrical surfaces will ensure minimal warping and consistent results. Finally, the company will offer resin mold repairs, from crack removal to finishing, on a single machine. This feature will accommodate hard-to-cut and high-hardness materials. Image: Rapidcncmachine Source: 3dprint
Cut to size plastic and acrylic fabrication
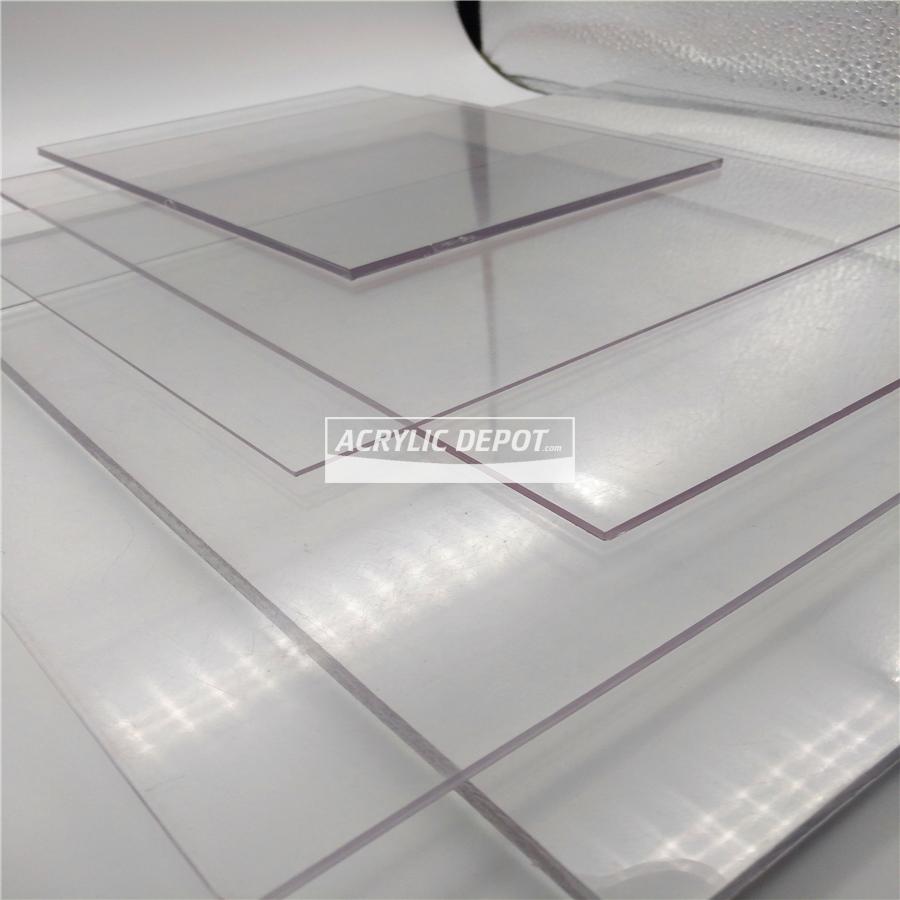
Uses for Plastic Sheeting Acrylic is incredibly versatile and has a wide range of uses. Many household projects and home improvements benefit from colored or clear plastic sheets. For example, homeowners often use high-impact, shatterproof acrylic as a cost-effective and safer alternative to glass for shed or greenhouse windows. Other popular uses include kitchen splashbacks, countertops, table protectors, and picture framing. Larger projects, such as shower tanking and wet-room installations, have also become increasingly common. These durable and stylish sheets can be cut to any size and come in virtually any color, making them both practical and fashionable. Colors and Other Options In addition to clear acrylic (equivalent to Acrylite®), we offer a wide range of colored plastics, including silver and gold mirror finishes. Our plastic sheets (acrylic and polycarbonate) are available in both transparent and opaque varieties. Simply provide the dimensions, color, thickness, and transparency preferences for your custom acrylic sheet order. Cut to Size After receiving your order, we cut and finish the edges of your bespoke plastic sheet to meet your exact requirements. We then wrap and protect your sheets to ensure they arrive at your door in pristine condition. Acrylic sheeting offers several advantages over other materials. It is lightweight, easy to clean and maintain, and can be molded into almost any shape. These qualities make acrylic sheets a perfect choice for various creative and functional projects. From Simple Shapes to Complex Designs We don’t just cut acrylic sheets to size; we also shape them into complex designs. Using state-of-the-art industrial plastic cutting machines, we deliver precise results based on your submitted design and special instructions. Whether you need simple shapes or intricate patterns, we can create exactly what you envision. Applications for Acrylic Sheets Cut-to-order acrylic sheets are ideal for countless applications at home, in offices, schools, and businesses. They are commonly used to replace display cabinet glazing, interior glass panels, walls, windows, and cupboard doors. Acrylic mirror-finished sheets are especially popular in gyms and home fitness studios as they provide a lightweight, cost-effective alternative to traditional glass mirrors. Outdoors, plastic sheets are frequently used for garden mirrors or as replacements for shed and greenhouse windows. While not unbreakable, acrylic sheets offer significantly higher impact resistance than glass and do not shatter into dangerous shards, making them a safer option. If safety is a concern, acrylic is the ideal choice. Plastic sheet is also incredibly easy to clean, maintain and cheap to replace if it becomes damaged. And being able to buy online with delivery anywhere in the Canada makes it an easy and convenient material to use in all sorts of applications, no matter how large or small. A.L.Plastics | Marion Collection | Acrylic Depot
Custom Plastics Machining
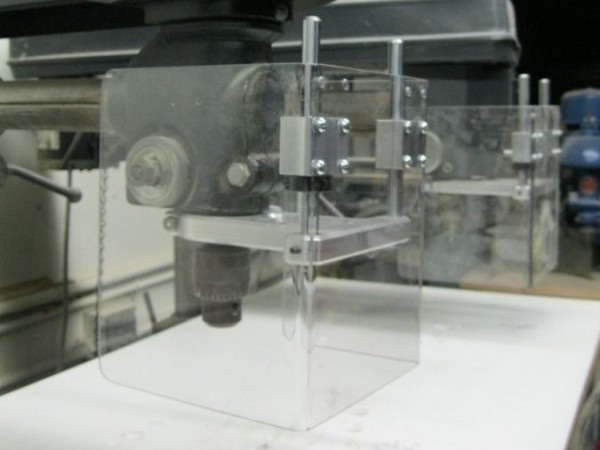
Custom Plastics Machining: What to Look for in a Supplier 1. Technology base It will always be preferable to work with suppliers who have the latest CNC production technology allied to skilled workers. These suppliers will be able to produce parts to close tolerances while keeping part quality and finish consistently high. 2. Materials expertise and selection There are a wide variety of plastic materials available on the market today. The best suppliers know their materials and know the latest materials available on the marketplace. These suppliers will be able to provide superior guidance on material selection, ensuring that the right material is chosen for a given application. Choosing the wrong material, or a material which is not exactly right, can result in misapplication challenges later on. 3. Application expertise in custom plastics machining Material knowledge is one thing, application knowledge is another. The latter should always precede the latter. Choose a supplier who knows how to undertake a comprehensive application review to determine how a finished part will be used. A good application review will identify all the requirements that the finished part must satisfy, and is critical for ensuring that the right material is chosen. In addition, some suppliers will specialize in serving a narrow range of industry applications, while other suppliers will serve a broader range. It is important to choose a supplier who has experience in serving your particular application – choosing a supplier with limited experience in servicing your specific application may increase the risk of misapplication issues arising post-sale. A.L.Plastics | Marion Collection | Acrylic Depot